Comprehensive Guide: Integrating PowerMill Ultimate with Other Software
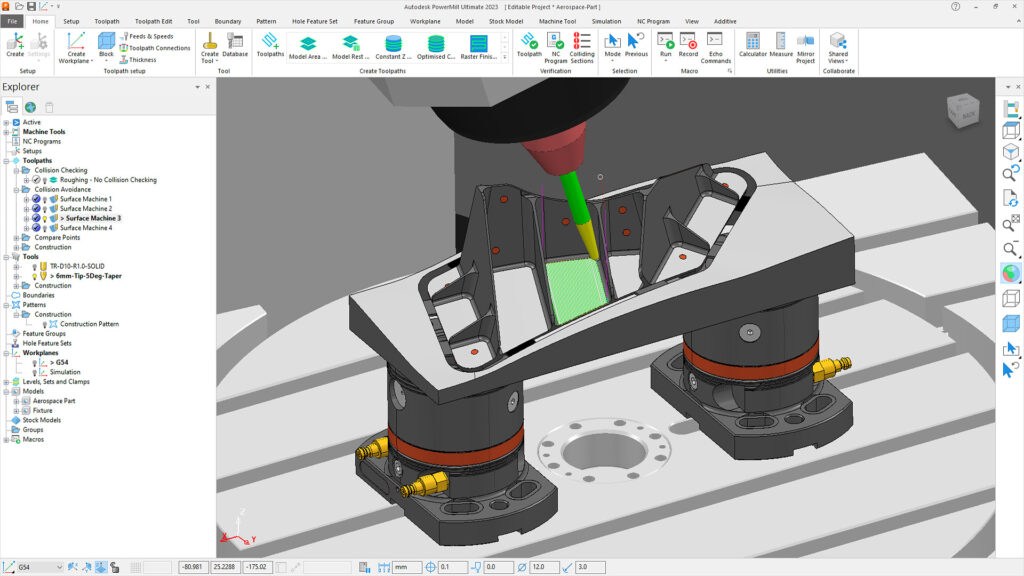
In today’s highly interconnected digital landscape, software integration has become a cornerstone of efficiency and productivity across industries. For manufacturers and engineers, the seamless integration of various software tools is crucial for streamlining workflows, enhancing collaboration, and maximizing the potential of each application. Among the leading software solutions in the realm of Computer-Aided Manufacturing (CAM), Autodesk’s PowerMill Ultimate stands out for its advanced capabilities in CNC machining and toolpath optimization. However, its true potential can be fully realized when integrated with complementary software across the design and manufacturing spectrum.
This comprehensive guide aims to explore the intricacies of integrating PowerMill Ultimate with other software, highlighting the benefits, challenges, and best practices associated with such endeavors. Whether you’re a seasoned professional seeking to optimize your manufacturing processes or a novice looking to harness the full power of your software suite, this article will serve as your roadmap to successful integration.
Understanding PowerMill Ultimate
Before delving into the integration aspects, it’s essential to grasp the fundamental features and functionalities of PowerMill Ultimate. Developed by Autodesk, PowerMill Ultimate is a high-performance CAM software designed for generating complex toolpaths for 3- and 5-axis CNC milling machines. It offers a wide range of advanced machining strategies, including high-speed machining, 5-axis machining, and robotics programming, making it indispensable for industries such as aerospace, automotive, and mold and die manufacturing.
Key features of PowerMill Ultimate include:
- Toolpath Optimization: PowerMill Ultimate employs sophisticated algorithms to optimize toolpaths for efficient material removal and surface finish.
- Simulation and Verification: Users can simulate machining operations to detect errors, collisions, and toolpath inefficiencies before sending programs to the machine.
- Additive Manufacturing Support: With the rise of additive manufacturing technologies, PowerMill Ultimate integrates additive and subtractive processes seamlessly, enabling hybrid manufacturing workflows.
- Robot Programming: The software facilitates the programming of robotic machining and material removal, expanding its applicability beyond traditional CNC machines.
The Need for Integration
While PowerMill Ultimate offers a robust set of features for CAM programming and toolpath optimization, its integration with other software extends its functionality and enhances the overall manufacturing process. Several factors drive the need for integration:
- Design Consistency: Integrating PowerMill Ultimate with CAD software ensures seamless data transfer, maintaining design integrity throughout the manufacturing process.
- Workflow Efficiency: By connecting PowerMill Ultimate with other manufacturing software, such as ERP (Enterprise Resource Planning) systems or PLM (Product Lifecycle Management) solutions, manufacturers can automate data exchange, reducing manual intervention and streamlining workflows.
- Collaboration and Communication: Integration enables real-time collaboration between design, engineering, and manufacturing teams, fostering communication and ensuring alignment throughout the product development lifecycle.
- Data Accessibility: Integrating PowerMill Ultimate with data management platforms allows for centralized storage and retrieval of machining data, facilitating version control, and ensuring data security.
Integration Challenges
While the benefits of integration are evident, the process is not without its challenges. Some common hurdles associated with integrating PowerMill Ultimate with other software include:
- Compatibility Issues: Different software applications may use proprietary file formats or data structures, leading to compatibility issues during integration.
- Data Synchronization: Ensuring data consistency and synchronization between software platforms can be challenging, especially when dealing with large datasets or complex geometries.
- Customization Requirements: Integration often requires customization or development of middleware solutions to facilitate data exchange and communication between disparate systems.
- Security Concerns: Sharing sensitive manufacturing data between software applications raises security concerns, necessitating robust encryption and access control mechanisms.
Best Practices for Integration
To overcome these challenges and maximize the benefits of integration, adhering to best practices is essential:
- Standardized Data Formats: Utilize standardized file formats such as STEP (Standard for the Exchange of Product Data) or IGES (Initial Graphics Exchange Specification) for seamless data exchange between PowerMill Ultimate and other software.
- API (Application Programming Interface) Integration: Leverage APIs provided by software vendors to enable direct communication and data transfer between PowerMill Ultimate and other applications.
- Middleware Solutions: Implement middleware solutions or custom plugins to bridge the gap between incompatible software platforms and facilitate data interoperability.
- Continuous Testing and Validation: Thoroughly test integration workflows to identify and address compatibility issues, data inconsistencies, and performance bottlenecks.
- Security Measures: Implement robust authentication, encryption, and access control mechanisms to safeguard sensitive manufacturing data during transit and storage.
Common Integration Scenarios
Integration of PowerMill Ultimate with other software can take various forms, depending on the specific requirements of the manufacturing process. Some common integration scenarios include:
- CAD-CAM Integration: Seamless integration between CAD software (e.g., Autodesk Inventor, SolidWorks) and PowerMill Ultimate enables direct import of 3D models and facilitates synchronized design and machining workflows.
- CAM-PLM Integration: Integration with Product Lifecycle Management (PLM) systems allows for automated data exchange between design, manufacturing, and quality assurance processes, ensuring traceability and compliance throughout the product lifecycle.
- ERP-CAM Integration: Integration with Enterprise Resource Planning (ERP) systems enables automatic generation of manufacturing orders, material requisitions, and production schedules based on CAM toolpaths and machining parameters.
- Simulation and Verification Integration: Integration with simulation software (e.g., Autodesk Fusion 360, Siemens NX) allows for comprehensive analysis and verification of machining operations, ensuring accuracy and minimizing errors before actual machining.
Case Studies
To illustrate the practical benefits of integration, let’s consider two hypothetical case studies:
Case Study 1: CAD-CAM Integration
A manufacturing company specializing in aerospace components integrates PowerMill Ultimate with Autodesk Inventor, its primary CAD software. This integration enables seamless transfer of 3D models from Inventor to PowerMill Ultimate, streamlining the CAM programming process and reducing design-to-production lead times by 30%.
Case Study 2: CAM-PLM Integration
A automotive OEM integrates PowerMill Ultimate with its PLM system to automate the generation of machining instructions and toolpath data from product designs. This integration ensures data consistency across design and manufacturing teams, leading to a 20% reduction in errors and rework during machining operations.
Conclusion
In conclusion, integrating PowerMill Ultimate with other software is essential for maximizing efficiency, productivity, and collaboration in modern manufacturing environments. By overcoming compatibility challenges, leveraging best practices, and embracing integration opportunities, manufacturers can unlock the full potential of their software investments and stay competitive in today’s rapidly evolving market landscape. Whether it’s CAD-CAM integration for design consistency or CAM-PLM integration for seamless data exchange, the benefits of integration are clear: optimized workflows, enhanced collaboration, and accelerated time-to-market. Embrace integration, and unleash the power of PowerMill Ultimate in your manufacturing endeavors.