How to Create and Manage Electrical Standards in Autodesk Electrical
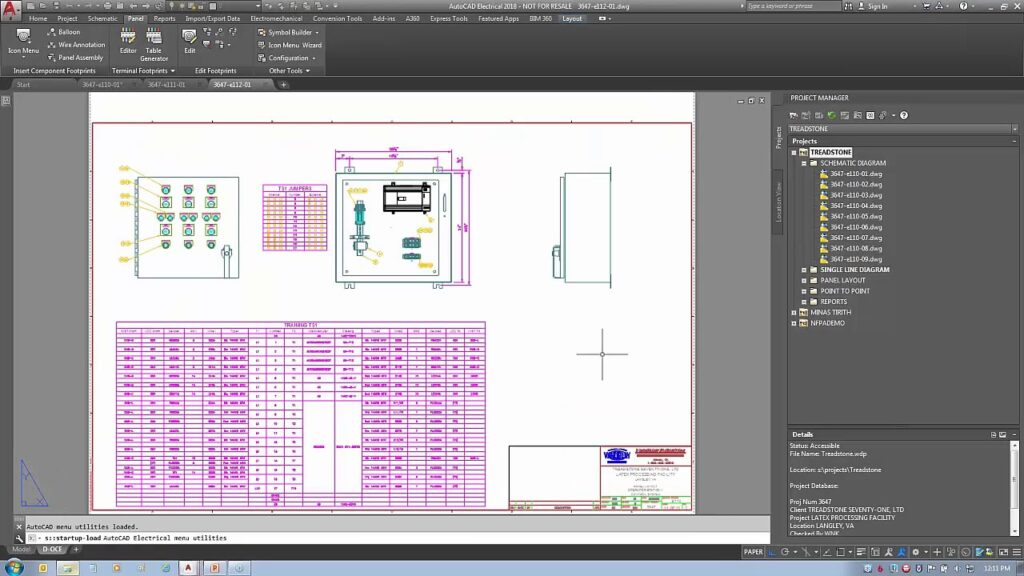
Autodesk Electrical is a powerful tool for electrical designers and engineers, offering a wide range of features to streamline the design process. One crucial aspect of using Autodesk Electrical effectively is establishing and managing electrical standards within the software. This comprehensive guide will walk you through the process of creating and managing electrical standards in Autodesk Electrical, covering everything from initial setup to ongoing maintenance.
Table of Contents
- Introduction
- 1.1 Overview of Autodesk Electrical
- 1.2 Importance of Electrical Standards
- 1.3 Objectives of this Guide
- Establishing Electrical Standards
- 2.1 Defining Electrical Components
- 2.2 Creating Symbol Libraries
- 2.3 Configuring Wire Styles
- 2.4 Setting Up Title Blocks and Drawing Templates
- Managing Electrical Standards
- 3.1 Version Control
- 3.2 Standard Updates and Revisions
- 3.3 Collaboration and Sharing
- Best Practices for Standardization
- 4.1 Consistency is Key
- 4.2 Documentation and Training
- 4.3 Regular Audits and Reviews
- Integration with Other Tools
- 5.1 AutoCAD Integration
- 5.2 PLC Software Integration
- 5.3 ERP/PLM Integration
- Troubleshooting and Support
- 6.1 Common Issues
- 6.2 Getting Help and Support
- Case Studies and Real-World Examples
- 7.1 Industry Case Studies
- 7.2 Lessons Learned
- Future Trends in Electrical Standards
- 8.1 Automation and AI
- 8.2 Cloud-Based Collaboration
- 8.3 Integration with IoT
1. Introduction
1.1 Overview of Autodesk Electrical
Autodesk Electrical is a specialized software solution for electrical design and documentation. It offers features such as schematic design, panel layout, PLC I/O design, and more. With its comprehensive set of tools, Autodesk Electrical enables engineers and designers to create accurate electrical drawings efficiently.
1.2 Importance of Electrical Standards
Establishing electrical standards is crucial for ensuring consistency, efficiency, and quality in electrical design projects. Standardization simplifies the design process, reduces errors, and facilitates collaboration among team members. By defining and adhering to electrical standards, organizations can improve productivity, minimize rework, and enhance the overall quality of their designs.
1.3 Objectives of this Guide
This guide aims to provide a comprehensive overview of creating and managing electrical standards in Autodesk Electrical. By following the guidelines outlined in this guide, users will learn how to establish standardized libraries, templates, and workflows within Autodesk Electrical. Additionally, best practices for managing and maintaining electrical standards will be discussed, along with tips for troubleshooting common issues and integrating with other tools and systems.
2. Establishing Electrical Standards
2.1 Defining Electrical Components
Before creating electrical standards in Autodesk Electrical, it’s essential to define the components that will be used in the design process. This includes standardizing symbols, footprints, manufacturer part numbers, and other relevant information. By defining these components upfront, designers can ensure consistency and accuracy in their drawings.
2.2 Creating Symbol Libraries
Symbol libraries are a central component of electrical standards in Autodesk Electrical. Designers can create custom symbol libraries containing predefined symbols for components such as relays, switches, motors, and more. These libraries can be organized hierarchically and categorized based on function, manufacturer, or other criteria.
2.3 Configuring Wire Styles
Wire styles define the appearance and properties of wires in Autodesk Electrical drawings. Designers can configure wire styles to specify attributes such as color, line type, and gauge. By standardizing wire styles, designers can ensure consistency in their drawings and make them easier to interpret.
2.4 Setting Up Title Blocks and Drawing Templates
Title blocks and drawing templates provide a standardized format for Autodesk Electrical drawings. Designers can create custom title blocks containing information such as project name, drawing number, revision history, and more. Drawing templates can be used to create new drawings with predefined settings, layout, and scale.
3. Managing Electrical Standards
3.1 Version Control
Version control is essential for managing electrical standards in Autodesk Electrical. Designers should establish procedures for tracking changes to symbol libraries, wire styles, title blocks, and drawing templates. This ensures that all team members are working with the latest versions of these standards and helps prevent errors and inconsistencies.
3.2 Standard Updates and Revisions
Electrical standards should be periodically reviewed and updated to reflect changes in design practices, industry standards, or organizational requirements. Designers should establish a process for managing updates and revisions to electrical standards, including documentation of changes and communication to team members.
3.3 Collaboration and Sharing
Collaboration tools within Autodesk Electrical enable team members to share and collaborate on electrical standards. Designers can use cloud-based storage solutions or PLM (Product Lifecycle Management) systems to store and share standard libraries, templates, and other resources. This facilitates collaboration among team members and ensures that everyone has access to the latest standards.
4. Best Practices for Standardization
4.1 Consistency is Key
Consistency is crucial when establishing electrical standards in Autodesk Electrical. Designers should strive to maintain consistency in symbols, wire styles, title blocks, and other elements across all drawings. This makes drawings easier to read and interpret and helps prevent errors and misinterpretations.
4.2 Documentation and Training
Documentation and training are essential aspects of managing electrical standards. Designers should document standardization procedures, guidelines, and best practices to ensure that team members understand and adhere to the established standards. Training programs should be provided to familiarize team members with the standardization process and the use of Autodesk Electrical tools.
4.3 Regular Audits and Reviews
Regular audits and reviews are necessary to ensure that electrical standards are being followed effectively. Designers should conduct periodic audits of drawings and documentation to identify any deviations from established standards. Reviews should be conducted with team members to solicit feedback and identify areas for improvement.
5. Integration with Other Tools
5.1 AutoCAD Integration
Autodesk Electrical integrates seamlessly with AutoCAD, allowing for easy sharing of drawings and standards between the two platforms. Designers can import/export drawings between AutoCAD Electrical and AutoCAD and use standard AutoCAD commands and tools within Autodesk Electrical.
5.2 PLC Software Integration
Autodesk Electrical also integrates with PLC (Programmable Logic Controller) software, enabling designers to exchange data between the two platforms. This allows for seamless integration of electrical schematics with PLC programming and facilitates communication between electrical and control systems.
5.3 ERP/PLM Integration
Integration with ERP (Enterprise Resource Planning) and PLM (Product Lifecycle Management) systems enables organizations to manage electrical standards alongside other product data. Designers can link Autodesk Electrical drawings and standards to items in the ERP/PLM system, ensuring that electrical data is synchronized with other product information.
6. Troubleshooting and Support
6.1 Common Issues
Common issues when creating and managing electrical standards in Autodesk Electrical include version control issues, compatibility issues