How to Perform a Static Structural Analysis in ANSYS
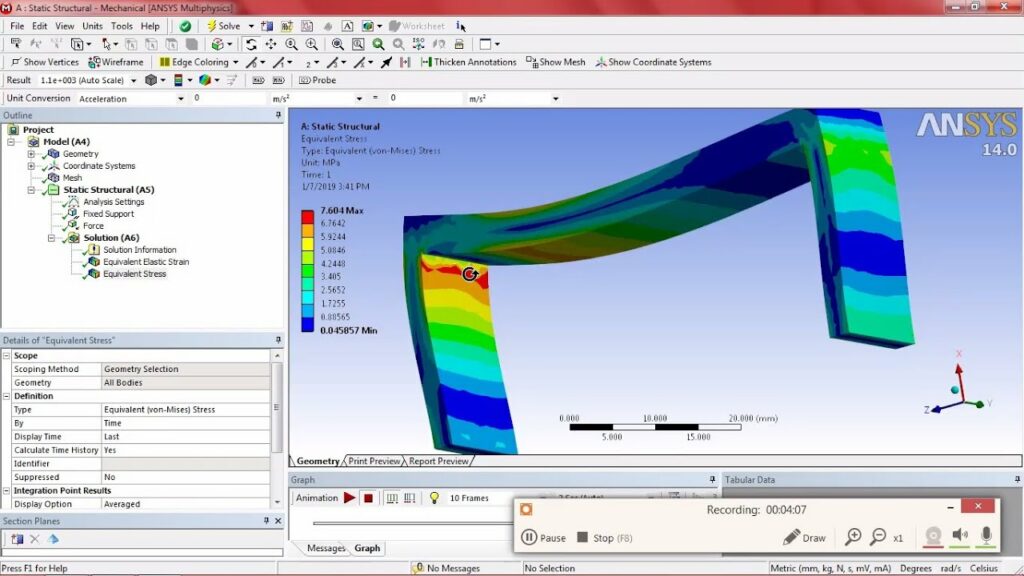
Performing a static structural analysis in ANSYS is a fundamental task for engineers and designers across various industries. This type of analysis helps in understanding how a structure or component responds to applied loads and constraints under static conditions. Whether you are analyzing a simple beam or a complex assembly, ANSYS provides powerful tools and capabilities to perform accurate static structural analyses. This comprehensive guide will walk you through the step-by-step process of setting up and conducting a static structural analysis using ANSYS, covering pre-processing, solution setup, post-processing, and interpretation of results.
Table of Contents
- Introduction to Static Structural Analysis
- Preparing Geometry for Analysis
- Applying Boundary Conditions
- Defining Material Properties
- Meshing the Model
- Setting Up Loads and Constraints
- Solving the Analysis
- Post-Processing and Analyzing Results
- Advanced Techniques and Considerations
- Troubleshooting and Common Issues
- Conclusion
1. Introduction to Static Structural Analysis
Static structural analysis in ANSYS involves evaluating the behavior of a structure when subjected to applied loads without considering dynamic effects such as inertia or damping. The analysis aims to determine stresses, strains, deformations, and displacements in the structure under steady-state conditions. This information is crucial for verifying the structural integrity, optimizing designs, and ensuring safety margins.
2. Preparing Geometry for Analysis
- Import CAD Geometry:
- Import the geometry of the structure or component into ANSYS.
- Supported formats include STEP, IGES, Parasolid, and native CAD formats.
- Clean Up Geometry:
- Remove unnecessary details and ensure the geometry is watertight and suitable for analysis.
- Use ANSYS DesignModeler or SpaceClaim for geometry cleanup if needed.
- Simplify Geometry:
- Simplify complex features or assemblies to reduce computational resources and enhance mesh quality.
3. Applying Boundary Conditions
- Fixed Constraints:
- Define fixed supports (fixed displacements) where the structure is rigidly constrained.
- Specify constraints such as zero displacement or rotation on selected surfaces or nodes.
- Loads:
- Apply loads such as forces, pressures, and moments to simulate external forces acting on the structure.
- Define load magnitudes, directions, and application points accurately.
4. Defining Material Properties
- Material Assignment:
- Assign appropriate material properties to the components of the model.
- Define material types (e.g., isotropic, orthotropic) and input material constants (e.g., Young’s modulus, Poisson’s ratio).
- Material Models:
- Choose material models that best represent the behavior of the materials under different loading conditions (e.g., linear elastic, nonlinear elastic).
5. Meshing the Model
- Mesh Generation:
- Generate a finite element mesh on the geometry using ANSYS Meshing or TGrid.
- Choose element types (e.g., tetrahedral, hexahedral) and refine the mesh in critical regions for accurate results.
- Mesh Quality:
- Ensure the mesh quality meets ANSYS recommended criteria (e.g., aspect ratio, skewness) for reliable analysis results.
- Use mesh controls to refine or coarsen the mesh locally based on geometric features and loading conditions.
6. Setting Up Loads and Constraints
- Load Application:
- Specify loads including forces, pressures, and moments acting on the structure.
- Define load directions, magnitudes, and application points accurately based on engineering requirements.
- Boundary Conditions:
- Apply boundary conditions such as fixed supports, rollers, or frictional contacts where the structure interacts with other components or supports.
7. Solving the Analysis
- Analysis Setup:
- Set up the static structural analysis in ANSYS Workbench.
- Configure solver settings including solution controls, convergence criteria, and solution methods (e.g., direct or iterative).
- Solver Execution:
- Launch the solver to perform the static structural analysis.
- Monitor the solver progress and convergence status to ensure the analysis completes successfully.
8. Post-Processing and Analyzing Results
- Result Visualization:
- Review and interpret analysis results using ANSYS Mechanical or Mechanical APDL.
- Visualize stress distribution, displacement contours, and deformation shapes to understand structural behavior.
- Result Evaluation:
- Evaluate safety factors, von Mises stresses, principal stresses, and other critical parameters to assess structural performance.
- Compare results against design criteria and standards to verify structural integrity.
9. Advanced Techniques and Considerations
- Nonlinear Analysis:
- Perform nonlinear static analyses to simulate large deformations, material nonlinearity, or contact interactions.
- Use advanced material models (e.g., plasticity, hyperelasticity) and nonlinear contact formulations.
- Dynamic Analysis:
- Consider dynamic effects by performing modal analyses or transient analyses to assess structural responses to time-varying loads.
10. Troubleshooting and Common Issues
- Convergence Issues:
- Address convergence problems by adjusting solver settings, refining the mesh, or improving load and boundary condition definitions.
- Mesh Quality Problems:
- Resolve mesh quality issues by refining the mesh, checking element aspect ratios, and using automatic mesh controls effectively.
11. Conclusion
Performing a static structural analysis in ANSYS involves a systematic approach from pre-processing to post-processing stages. By following the steps outlined in this guide, engineers and analysts can effectively simulate and analyze the behavior of structures under static loading conditions. Understanding the nuances of geometry preparation, material assignment, meshing, load application, and result interpretation is essential for obtaining accurate and reliable analysis results. ANSYS provides powerful tools and capabilities to handle complex structural analyses, making it a preferred choice for engineers across various industries seeking to optimize designs, ensure safety, and innovate with confidence.