Mastering Multiphase Flow Simulation in OpenFOAM: A Comprehensive Guide
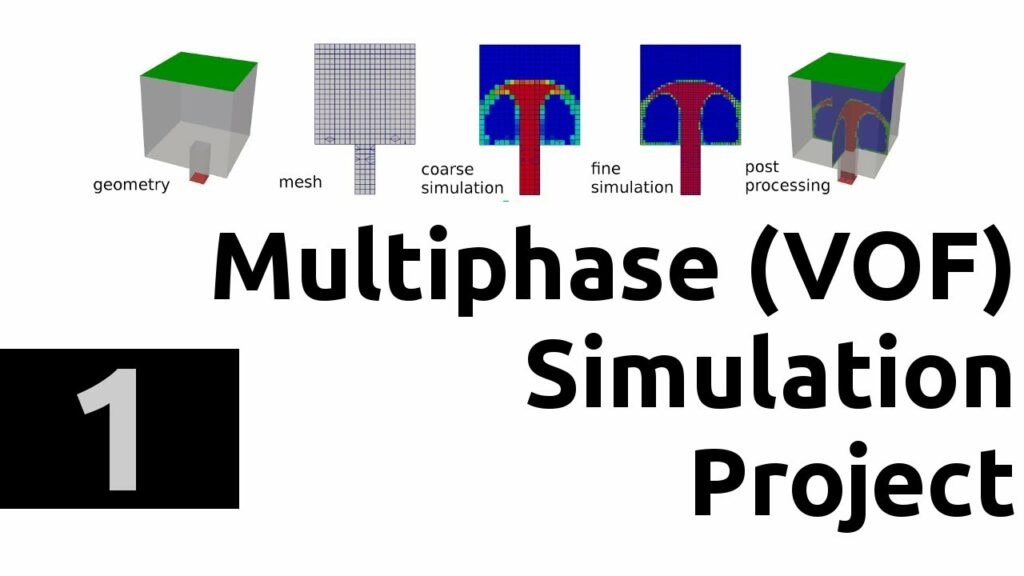
Introduction: Multiphase flows, characterized by the simultaneous movement of multiple phases (such as gas-liquid, liquid-liquid, or gas-solid) within a single system, are prevalent in various engineering applications, including petroleum engineering, chemical processing, environmental engineering, and more. OpenFOAM, an open-source computational fluid dynamics (CFD) software, provides a powerful platform for simulating multiphase flows with accuracy and efficiency. In this extensive guide, we will delve into the intricacies of simulating multiphase flows in OpenFOAM, covering fundamental concepts, modeling approaches, simulation setup, and advanced techniques.
Section 1: Understanding Multiphase Flows
1.1 Overview of Multiphase Flows: Multiphase flows involve the simultaneous flow of two or more immiscible fluids or phases within a single computational domain. The behavior of multiphase flows is governed by complex interactions between phases, including interfacial forces, phase change phenomena (such as evaporation or condensation), and mass transfer processes.
1.2 Classification of Multiphase Flows: Multiphase flows can be classified based on the distribution and characteristics of phases, including:
- Dispersed Flows: Where one phase is dispersed as droplets or bubbles within another continuous phase.
- Segregated Flows: Where phases are separated into distinct regions or layers within the domain.
- Stratified Flows: Where phases are stratified based on density differences, with heavier phases settling below lighter phases.
1.3 Challenges in Multiphase Flow Simulation: Simulating multiphase flows presents several challenges, including capturing phase interactions, resolving interfacial phenomena, modeling phase transitions, and predicting complex flow regimes accurately. OpenFOAM offers specialized solvers and models to address these challenges and enable robust multiphase flow simulations.
Section 2: Multiphase Flow Modeling in OpenFOAM
2.1 Volume of Fluid (VOF) Method: The Volume of Fluid method is a widely used approach for simulating multiphase flows in OpenFOAM. It tracks the volume fraction of each phase within computational cells, allowing for the representation of interface dynamics, phase distribution, and phase interaction phenomena. OpenFOAM provides VOF-based solvers such as interFoam and interDyMFoam for simulating dispersed multiphase flows with high fidelity.
2.2 Eulerian-Eulerian Multiphase Models: Eulerian-Eulerian models treat each phase as a continuous fluid with its own set of governing equations, making them suitable for simulating segregated and stratified multiphase flows. OpenFOAM offers solvers like multiphaseEulerFoam and multiphaseInterFoam based on Eulerian-Eulerian formulations, allowing engineers to model complex multiphase flow phenomena, including phase separation, phase entrainment, and phase distribution.
2.3 Eulerian-Lagrangian Multiphase Models: Eulerian-Lagrangian models combine an Eulerian description of the continuous phase with a Lagrangian description of dispersed phases (such as droplets or particles). OpenFOAM provides solvers like DPMFoam and LPTFoam for simulating dispersed multiphase flows using Eulerian-Lagrangian approaches, enabling engineers to model particle-laden flows, spray dynamics, and particle-particle interactions.
Section 3: Simulation Setup and Workflow
3.1 Geometry and Mesh Generation: The first step in simulating multiphase flows in OpenFOAM is to create a computational domain representing the physical geometry of the system. Engineers can use CAD software to design geometries and mesh generation tools like snappyHexMesh or blockMesh within OpenFOAM to generate structured or unstructured meshes suitable for multiphase flow simulations.
3.2 Boundary and Initial Conditions: Defining appropriate boundary and initial conditions is critical for accurately simulating multiphase flows. Engineers must specify inlet velocities, phase fractions, interfacial properties, and other boundary conditions based on the physics of the system and experimental data.
3.3 Solver Selection and Configuration: OpenFOAM provides a variety of solvers and models for simulating multiphase flows, each tailored to specific flow regimes and phenomena. Engineers should select the most appropriate solver and configure solver settings, numerical schemes, and convergence criteria based on the desired level of accuracy and computational efficiency.
3.4 Post-Processing and Visualization: Post-processing and visualization play a vital role in analyzing simulation results and gaining insights into multiphase flow behavior. OpenFOAM offers built-in tools like ParaView for visualizing flow fields, phase distributions, interfacial structures, and other simulation outputs in 2D and 3D formats.
Section 4: Advanced Techniques and Applications
4.1 Multiphase Heat Transfer: Multiphase flow simulations often involve heat transfer processes, such as boiling, condensation, and phase change heat transfer. OpenFOAM’s conjugate heat transfer capabilities, coupled with multiphase flow solvers, enable engineers to simulate complex heat transfer phenomena in multiphase systems accurately.
4.2 Multiphase Reacting Flows: Multiphase reacting flows arise in various engineering applications, including combustion, chemical processing, and environmental remediation. OpenFOAM’s reacting multiphase flow solvers, combined with combustion models and chemical kinetics mechanisms, enable engineers to study combustion processes, pollutant formation, and chemical reactions in multiphase environments.
4.3 Multiphase Turbulence Modeling: Turbulence is prevalent in multiphase flows and significantly influences flow behavior, phase dispersion, and interfacial dynamics. OpenFOAM offers turbulence models specifically designed for multiphase flows, such as the k-epsilon model, the k-omega SST model, and the Reynolds stress model, enabling engineers to accurately capture turbulent effects in multiphase flow simulations.
Section 5: Best Practices and Tips
5.1 Model Validation and Verification: Validating and verifying multiphase flow models is essential for ensuring the accuracy and reliability of simulation results. Engineers should compare simulation data with experimental measurements, analytical solutions, or empirical correlations to assess model accuracy and identify areas for improvement.
5.2 Sensitivity Analysis: Conducting sensitivity analysis helps engineers understand the impact of model parameters, boundary conditions, and numerical settings on simulation results. Engineers should systematically vary key parameters, assess their influence on simulation outcomes, and optimize model settings to improve predictive accuracy and robustness.
5.3 Collaboration and Knowledge Sharing: Multiphase flow simulation often requires interdisciplinary collaboration between engineers, scientists, and domain experts. Engineers should actively engage with colleagues, participate in research communities, and share knowledge and experiences to foster innovation, address challenges, and advance the state-of-the-art in multiphase flow simulation.
Conclusion: Simulating multiphase flows in OpenFOAM offers engineers a powerful toolset for understanding and analyzing complex fluid dynamics phenomena in engineering applications. By mastering the fundamental concepts, modeling approaches, and simulation techniques discussed in this guide, engineers can tackle diverse multiphase flow problems with confidence and precision. With OpenFOAM’s flexibility, extensibility, and robustness, engineers can push the boundaries of multiphase flow simulation, drive innovation, and make meaningful contributions to engineering research and practice.