Mastering Toolpath Reports: A Comprehensive Guide
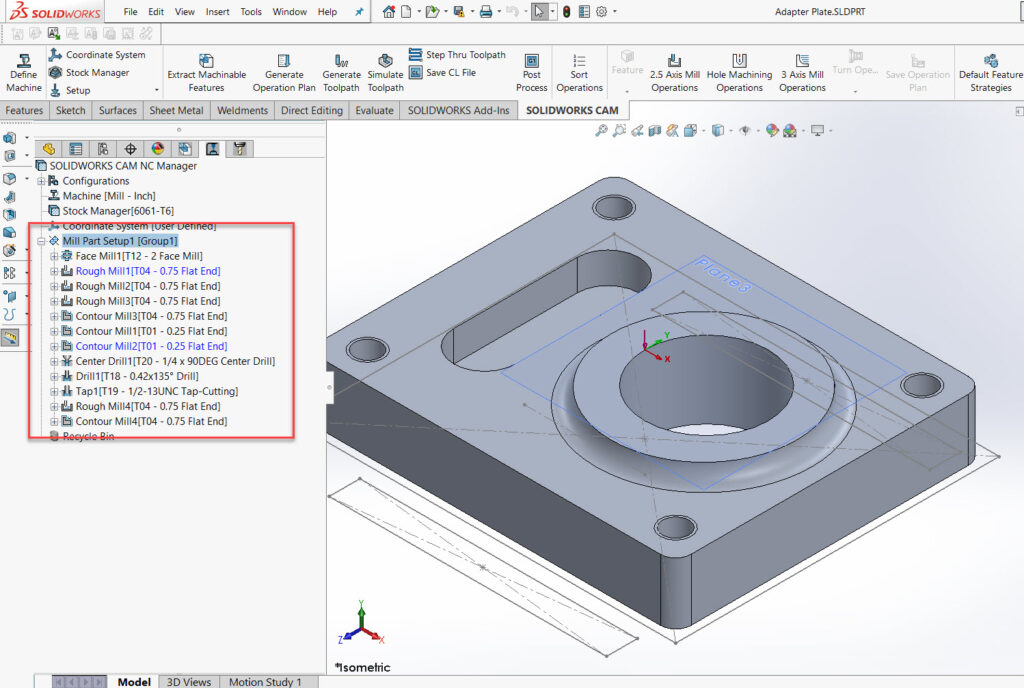
In the realm of computer-aided manufacturing (CAM), generating toolpath reports is an essential step in the machining process. These reports provide vital information about toolpaths, cutting parameters, tool usage, and material removal rates, enabling manufacturers to optimize machining operations, troubleshoot issues, and ensure quality control. In this comprehensive guide, we’ll delve into the intricacies of generating toolpath reports, exploring the importance, components, methods, and best practices associated with this critical aspect of CAM programming.
Understanding Toolpath Reports
Before diving into the details of generating toolpath reports, it’s crucial to understand their significance and purpose. Toolpath reports serve as comprehensive documentation of the machining process, capturing essential data points such as:
- Toolpath Geometry: Detailed information about the trajectory followed by the cutting tool during machining operations.
- Cutting Parameters: Parameters such as feed rate, spindle speed, depth of cut, and stepover distance used during toolpath generation.
- Tool Information: Specifications of the cutting tool utilized, including tool diameter, tool type, tool material, and tool life.
- Material Removal Rates (MRR): Quantitative data on the rate at which material is removed during machining, aiding in process optimization and cycle time estimation.
- Collision Detection: Identification of any collisions or toolpath errors encountered during simulation or machining, facilitating troubleshooting and error correction.
Importance of Toolpath Reports
Toolpath reports play a pivotal role in the manufacturing process, offering several key benefits:
- Process Optimization: By analyzing toolpath reports, manufacturers can identify inefficiencies, optimize cutting parameters, and improve machining performance to achieve higher productivity and better surface finish.
- Quality Assurance: Toolpath reports provide a detailed record of machining operations, enabling manufacturers to verify adherence to design specifications, tolerances, and quality standards.
- Documentation and Traceability: Toolpath reports serve as valuable documentation of the manufacturing process, facilitating traceability, auditing, and compliance with regulatory requirements.
- Troubleshooting and Error Analysis: In the event of machining errors or toolpath collisions, toolpath reports provide valuable insights for troubleshooting and error analysis, aiding in rapid resolution and minimizing downtime.
- Communication and Collaboration: Toolpath reports serve as a communication tool between design, engineering, and manufacturing teams, ensuring alignment and clarity throughout the product development lifecycle.
Components of Toolpath Reports
Toolpath reports typically contain several key components, each providing valuable insights into the machining process:
- Header Information: Includes details such as the project name, part number, revision, date of creation, and the name of the CAM programmer responsible for generating the toolpath.
- Toolpath Visualization: Graphical representation of the toolpath trajectory overlaid on the part geometry, providing a visual understanding of the machining operations.
- Cutting Parameters Table: A tabular summary of cutting parameters used during toolpath generation, including feed rate, spindle speed, depth of cut, stepover distance, and coolant settings.
- Tool Information: Specifications of the cutting tool utilized for machining, including tool type, tool diameter, tool material, tool life, and any additional tool-related parameters.
- Material Removal Rates (MRR): Quantitative data on material removal rates for different regions of the part geometry, facilitating analysis of machining efficiency and cycle time estimation.
- Simulation Results: Summary of simulation results, including collision detection, toolpath verification, and any warnings or errors encountered during simulation.
- Notes and Comments: Space for the CAM programmer to provide additional comments, annotations, or recommendations related to the toolpath or machining process.
Methods for Generating Toolpath Reports
Generating toolpath reports can be accomplished using various methods, depending on the CAM software used and the specific requirements of the manufacturing process:
- Built-in Reporting Tools: Many CAM software packages include built-in reporting tools that allow users to generate customized toolpath reports directly from the CAM environment. These tools typically offer templates, customizable layouts, and export options for generating reports in various formats, such as PDF, Excel, or HTML.
- Post-Processing Scripts: CAM programmers can develop custom post-processing scripts or macros to extract relevant data from the CAM environment and generate customized toolpath reports tailored to specific requirements. This approach offers flexibility and automation but requires programming expertise.
- Third-Party Plugins: Some CAM software platforms support third-party plugins or extensions that extend the functionality of the software, including advanced reporting capabilities. CAM programmers can explore available plugins or develop custom integrations to enhance reporting capabilities.
- Manual Documentation: In cases where automated reporting tools are not available or practical, CAM programmers can manually document toolpath information using spreadsheets, word processors, or other documentation tools. While less efficient, manual documentation can still provide valuable insights into the machining process.
Best Practices for Generating Toolpath Reports
To ensure the effectiveness and reliability of toolpath reports, it’s essential to adhere to best practices:
- Standardization: Establish standardized templates, formats, and naming conventions for toolpath reports to ensure consistency and facilitate comparison across different machining projects.
- Automation: Whenever possible, automate the generation of toolpath reports using built-in reporting tools, post-processing scripts, or third-party plugins to minimize manual effort and reduce the risk of errors.
- Data Accuracy: Verify the accuracy and completeness of toolpath data before generating reports, ensuring that cutting parameters, tool information, and simulation results are correctly captured and documented.
- Customization: Tailor toolpath reports to meet the specific requirements of stakeholders, incorporating relevant metrics, visualization, and annotations to provide actionable insights and facilitate decision-making.
- Version Control: Implement version control mechanisms to track changes and revisions to toolpath reports over time, ensuring traceability and auditability of machining processes.
- Documentation Management: Store toolpath reports and associated documentation in a centralized repository or document management system for easy access, retrieval, and sharing among stakeholders.
- Continuous Improvement: Regularly review and evaluate toolpath reports to identify areas for improvement, refine reporting templates, and incorporate feedback from stakeholders to enhance the effectiveness of reporting processes.
Conclusion
In conclusion, generating toolpath reports is a critical aspect of the CAM programming process, providing valuable insights into machining operations, optimizing cutting parameters, and ensuring quality control. By understanding the importance, components, methods, and best practices associated with toolpath reports, manufacturers can leverage this essential tool to streamline workflows, enhance collaboration, and achieve manufacturing excellence. Whether it’s automated reporting tools, custom post-processing scripts, or manual documentation, the key is to harness the power of toolpath reports to drive continuous improvement and innovation in CAM programming. Master the art of generating toolpath reports, and unlock the full potential of your machining operations.