Mastering Toolpath Verification: A Comprehensive Guide
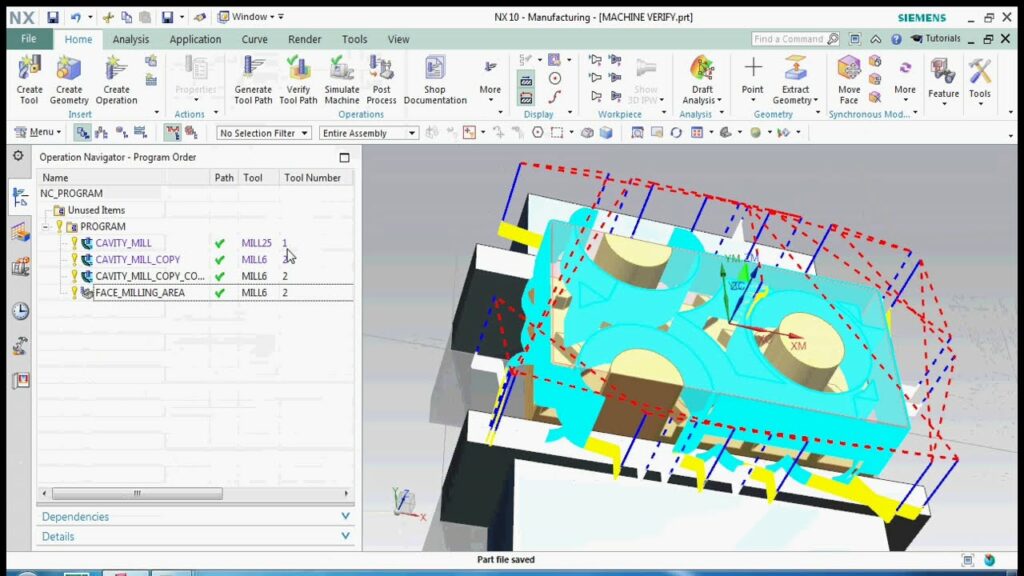
In the realm of computer-aided manufacturing (CAM), toolpath verification is an essential step in ensuring the accuracy, reliability, and safety of machining operations. Toolpath verification involves simulating and analyzing the motion of cutting tools along programmed toolpaths to detect errors, collisions, and deviations from intended machining trajectories. By thoroughly verifying toolpaths before actual machining, manufacturers can identify and mitigate potential issues, resulting in improved part quality, reduced scrap rates, and increased productivity. In this comprehensive guide, we’ll explore the importance, methods, challenges, and best practices associated with performing toolpath verification.
Understanding Toolpath Verification
Before delving into the details of toolpath verification, it’s essential to understand its significance and purpose. Toolpath verification serves several critical functions:
- Error Detection: Toolpath verification allows manufacturers to detect errors, inconsistencies, and inaccuracies in toolpaths before machining, preventing costly mistakes and rework.
- Collision Avoidance: By simulating the motion of cutting tools within the machining envelope of the machine tool, toolpath verification helps identify potential collisions between the tool, toolholder, workpiece, fixtures, and machine components.
- Accuracy Assessment: Verifying toolpaths enables manufacturers to assess the accuracy and precision of machining operations, ensuring adherence to design specifications and tolerances.
- Process Optimization: Through simulation and analysis of toolpaths, manufacturers can optimize cutting parameters, toolpath strategies, and machining sequences to maximize efficiency and quality.
Importance of Toolpath Verification
Toolpath verification is of paramount importance for several reasons:
- Quality Assurance: Verifying toolpaths ensures that machining operations meet quality standards and produce parts that conform to design specifications and tolerances.
- Risk Mitigation: By identifying and addressing potential errors and collisions in toolpaths before machining, manufacturers reduce the risk of damage to cutting tools, workpieces, fixtures, and machine components.
- Time and Cost Savings: Detecting and correcting errors during toolpath verification minimizes downtime, scrap rates, and rework, resulting in cost savings and improved productivity.
- Compliance and Safety: Toolpath verification helps ensure compliance with safety regulations and industry standards, mitigating risks associated with machine tool operation and workplace safety.
Methods for Performing Toolpath Verification
Toolpath verification can be performed using various methods, each with its advantages, limitations, and applicability:
- Simulation Software: Dedicated CAM software packages often include built-in toolpath verification capabilities that allow users to simulate tool motion, visualize toolpaths, and detect collisions within a virtual machining environment.
- Machine Tool Simulation: Some CAM software solutions offer machine tool simulation modules that provide a more accurate representation of machine tool kinematics, including axis movements, tool changes, and spindle rotations, enabling realistic toolpath verification.
- Virtual Machining Platforms: Virtual machining platforms combine CAM software with physics-based simulation engines to provide comprehensive toolpath verification, including dynamic analysis of cutting forces, material removal, and tool wear.
- Third-Party Verification Tools: In addition to built-in verification tools, third-party software solutions and plugins are available for specialized analysis, such as thermal simulation, chip evacuation, and surface finish prediction.
- Post-Processing Verification: After generating toolpaths, manufacturers can export G-code or machine-specific NC programs and use machine simulation software or CNC machine controllers to verify toolpaths directly on the machine tool.
Challenges and Considerations
Performing toolpath verification poses several challenges and considerations that must be addressed to ensure accurate and reliable results:
- Simulation Accuracy: Achieving accurate toolpath verification requires precise modeling of cutting tools, workpiece materials, machine kinematics, and cutting conditions, as well as consideration of factors such as tool wear and deformation.
- Computational Resources: Complex simulations involving large CAD models, fine meshing, and dynamic analysis can be computationally intensive and may require significant processing power and memory resources.
- Collision Detection: Accurately detecting collisions between the tool, workpiece, fixtures, and machine components requires robust collision detection algorithms and collision models that account for geometric complexity and kinematic constraints.
- Model Validation: Validating simulation results against experimental data or benchmark cases is essential for verifying the accuracy and reliability of simulation models and ensuring confidence in verification results.
- Iterative Optimization: Integrating toolpath verification into an iterative design and manufacturing process allows manufacturers to refine toolpaths, optimize cutting parameters, and validate machining strategies iteratively to achieve optimal results.
Best Practices for Toolpath Verification
To maximize the effectiveness and reliability of toolpath verification, manufacturers should adhere to best practices:
- Pre-Processing Preparation: Ensure that CAD models, tool geometries, workpiece setups, and cutting parameters are accurately defined and properly imported into the simulation environment before performing verification.
- Iterative Analysis: Conduct iterative verification and optimization cycles, refining toolpaths, adjusting cutting parameters, and validating machining strategies to achieve desired results iteratively.
- Comprehensive Analysis: Perform comprehensive analysis of toolpaths, including collision detection, surface finish prediction, chip evacuation analysis, and dynamic cutting force simulation, to assess and optimize machining performance comprehensively.
- Post-Processing Review: Review simulation results, analyze critical areas of concern, and generate reports summarizing verification findings, recommendations for improvement, and validation results for documentation and future reference.
- Continuous Improvement: Continuously monitor and evaluate toolpath verification processes, incorporate feedback from simulation results and machining experiences, and update simulation models and methodologies to drive continuous improvement in machining performance.
Applications and Case Studies
Toolpath verification finds applications across various industries and machining processes:
- Milling Operations: Verifying toolpaths in milling operations helps optimize cutting strategies, detect collisions, and ensure part accuracy and surface finish in complex geometries and multi-axis machining.
- Turning Operations: In turning operations, toolpath verification aids in optimizing tool movements, minimizing tool deflection, and maximizing machining efficiency while maintaining dimensional accuracy and surface quality.
- Drilling and Hole Making: Verifying toolpaths in drilling and hole-making processes enables manufacturers to ensure hole alignment, depth control, and chip evacuation while avoiding tool breakage and workpiece damage.
- Multi-Tasking Machining: Toolpath verification is essential for multi-tasking machining centers, where multiple cutting tools operate simultaneously on different surfaces, requiring careful coordination and collision avoidance.
Conclusion
In conclusion, performing toolpath verification is a critical aspect of CAM programming and machining preparation, enabling manufacturers to ensure the accuracy, reliability, and safety of machining operations. By leveraging simulation software, machine tool simulation, virtual machining platforms, and third-party verification tools, manufacturers can detect errors, prevent collisions, optimize cutting parameters, and validate machining strategies effectively. By adhering to best practices, addressing challenges, and applying toolpath verification across various machining processes, manufacturers can achieve superior part quality, reduce scrap rates, increase productivity, and enhance competitiveness in today’s manufacturing landscape. Master the art of toolpath verification, and unlock the full potential of your machining capabilities.